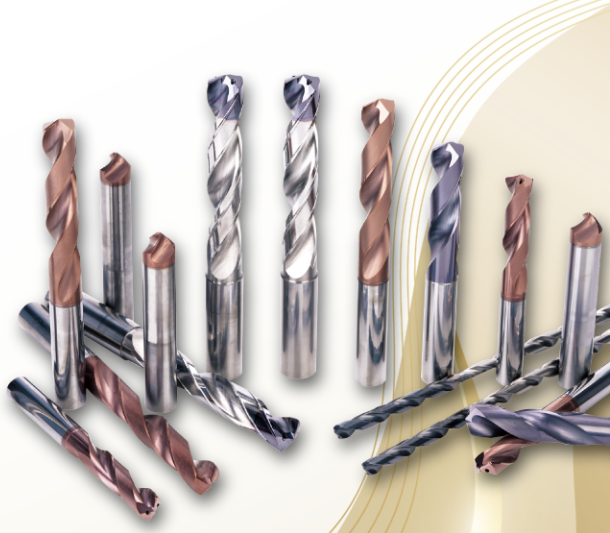
Professional-Grade Tungsten Carbide Drill Recommendations | The Best Choice for Efficient and Precise Machining
As a mechanical machining enthusiast, I am always searching for tools to improve efficiency and precision. Tungsten carbide drills have proven to be the best choice for me. Their hardness and wear resistance make my work more precise and efficient.
The advantages of tungsten carbide drills extend beyond their physical properties. They excel in various applications, whether working with metals, wood, or stone. Tungsten carbide drills are essential tools for anyone who values high-quality machining.
________________________________________
Key Points
- Tungsten carbide drills feature exceptional hardness and wear resistance.
- They enable precise and efficient machining.
- Suitable for processing a wide range of materials, including metal, wood, and stone.
- A top choice for professional machinists.
- Significantly improve work efficiency and accuracy.
________________________________________
Advantages and Features of Tungsten Carbide Drills
Tungsten carbide drills are professional-grade machining tools with numerous benefits. Their high hardness and wear resistance are attributed to their composition of tungsten carbide material.
This material ensures that the drills maintain their sharpness even after prolonged use. This not only enhances machining precision but also extends the tool's lifespan.
High Hardness and Wear Resistance
Tungsten carbide drills are made from a specialized tungsten carbide alloy with hardness levels reaching 2000-2500 HV. This makes them 2-3 times more wear-resistant than traditional high-speed steel drills.
Even when processing high-strength metals for extended periods, the cutting edges of the drills remain sharp, ensuring consistently high machining standards.
Key Factors for Precision Machining
The material hardness and wear resistance of drills are crucial for achieving precision machining. Tungsten carbide drills perform excellently in metalworking and wood drilling, ensuring high-quality results and improved machining efficiency.
Applications and Fields of Use
- Metalworking: Precise drilling of hard metals such as steel, aluminum alloys, and copper.
- Woodworking: High-quality drilling for furniture and wood components.
- Composite Material Processing: Cutting and drilling of emerging composite materials like carbon fiber and fiberglass.
Whether for metalworking or wood drilling, tungsten carbide drills ensure efficient and accurate machining quality, making them the preferred tools for professionals.
________________________________________
Key Considerations When Choosing Professional Tungsten Carbide Drills
Selecting tungsten carbide drills requires considering several factors. The most critical ones include drill size, edge design, and coating technology. Brand reputation and cost-effectiveness are also essential. Let’s dive into these key factors.
- Drill Size: Drill size is a primary consideration when purchasing. Different sizes suit different machining needs. Smaller sizes are ideal for delicate work, while larger sizes are better for rough machining. Choosing the wrong size can affect both machining quality and efficiency.
- Edge Design: The edge design directly impacts the cutting performance of the drill. Different cutting tasks require specific edge designs. Choosing the right edge design enhances cutting efficiency and extends tool life.
- Coating Technology: Advanced coating technologies can improve the hardness and wear resistance of drills. Common coatings include titanium nitride (TiN) and titanium aluminum nitride (TiAlN). These coatings reduce friction and extend the tool’s lifespan.
Choosing a reputable brand is crucial as they provide high-quality products and excellent after-sales service. Balancing budget considerations with quality will help you find cost-effective drills. Only by considering all factors can you find professional-grade tungsten carbide drills that meet your needs.
________________________________________
Conclusion
Professional-grade tungsten carbide drills are key to improving machining efficiency and quality. Their exceptional hardness and wear resistance ensure precise and reliable machining performance, suitable for various materials and industries.
Choosing the right tungsten carbide drill enhances production efficiency and provides a great return on investment.
As a professional, I place great importance on the quality and performance of my tools. Selecting tungsten carbide drills is a smart decision. Their precision machining capabilities and excellent user experience will boost your work efficiency and deliver outstanding results.
No matter your industry, owning tungsten carbide drills is a worthwhile investment. They open new opportunities for professional machining.
By selecting the right tungsten carbide drills, I am confident you can improve productivity and achieve better returns on your investment. Let’s explore the limitless possibilities of tungsten carbide drills and start a new chapter in your professional machining journey.
________________________________________
Frequently Asked Questions (FAQ)
Q1: What are tungsten carbide drills, and what are their advantages?
A1: Tungsten carbide drills are made from ultra-hard materials like tungsten carbide. They are extremely hard and wear-resistant, capable of precise machining across various materials. Compared to standard drills, they are more durable and improve work efficiency.
Q2: In which fields are tungsten carbide drills commonly used?
A2: Tungsten carbide drills are widely used in industries such as mechanical manufacturing and automotive parts processing. Their high hardness and wear resistance make machining more precise and reliable. They are the go-to choice for both large equipment repairs and small component production.
Q3: What factors should be considered when purchasing tungsten carbide drills?
A3: When purchasing tungsten carbide drills, consider the following:
1. Size and shape: Choose the appropriate size and design for your needs.
2. Coating technology: Advanced coatings enhance wear resistance and lifespan.
3. Brand and quality: Opt for reputable brands and reliable suppliers to ensure quality.
4. Cost-effectiveness: Select products that meet your needs while offering good value.
Q4: How can I maximize the performance of tungsten carbide drills?
A4: To fully utilize the advantages of tungsten carbide drills, pay attention to:
1. Choosing the right parameters, such as speed and feed rate, based on the material.
2. Adjusting cutting angles and edge designs to improve cutting efficiency.
3. Maintaining and cleaning tools regularly to extend their lifespan.
4. Pairing them with advanced equipment and techniques to unlock their full potential.